add life to buildings
Cross Lock spacers & rebar chairs / PVC cover block has a unique self locking system and high load bearing capacity.
It ensures perfect concrete, strength safety and durability of buildings.

Advantages of Cross lock spacers & Rebar chairs
Self-locking, Non-rotating
Crosslock spacers and rebar chairs are self-locking and non-rotating, which means that they cannot be accidentally displaced during casting. This ensures that the concrete is poured evenly and the steel bars are properly protected.
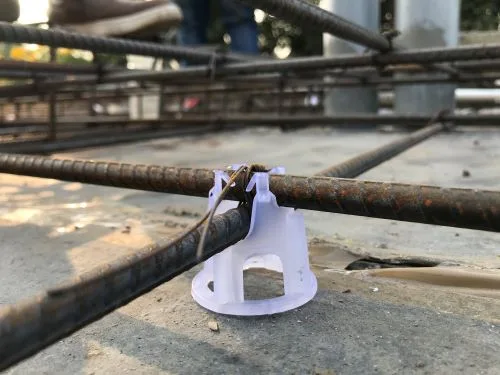
Fill inside out system
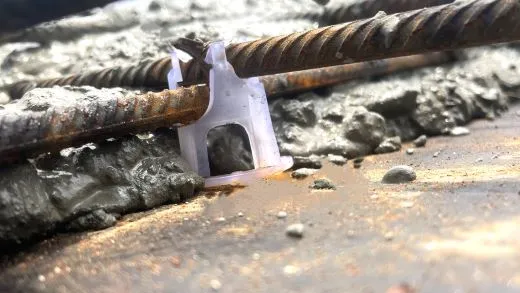
Concrete flows through large holes of Crosslock spacers and rebar chairs. This means a homogeneous structure where spacer becomes part of structure without cold joint formation.
Lightweight – High Strength
Crosslock spacers and rebar chairs are made from high-strength polypropylene, but they are also very lightweight. This makes them easy to handle and transport. It has got strength of 4 Kn which makes them best performing cover blocks.
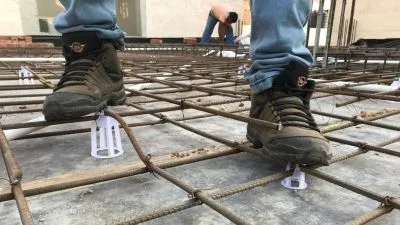
Non porous – Chemically inert
Unlike traditional site made mortar blocks crosslock spacers and rebar chairs are non-porous which means that moisture cannot pass through them. They are chemically inert in concrete. Unlike mortar blocks they are immune from carbonation effects.
Precise clear cover under steel bars
Crosslock spacers and rebar chairs help to maintain a uniform gap under the steel bars. This is important for ensuring that the concrete has an accurate clear cover over the steel bars. This is essential for the strength and durability of concrete structures.
Protect steel bars from corrosion
Proper concrete cover creates a passive alkaline layer under steel bars. This passive layer of concrete helps in preventing corrosion of steel bars.
Smooth surfaces due to non visibility
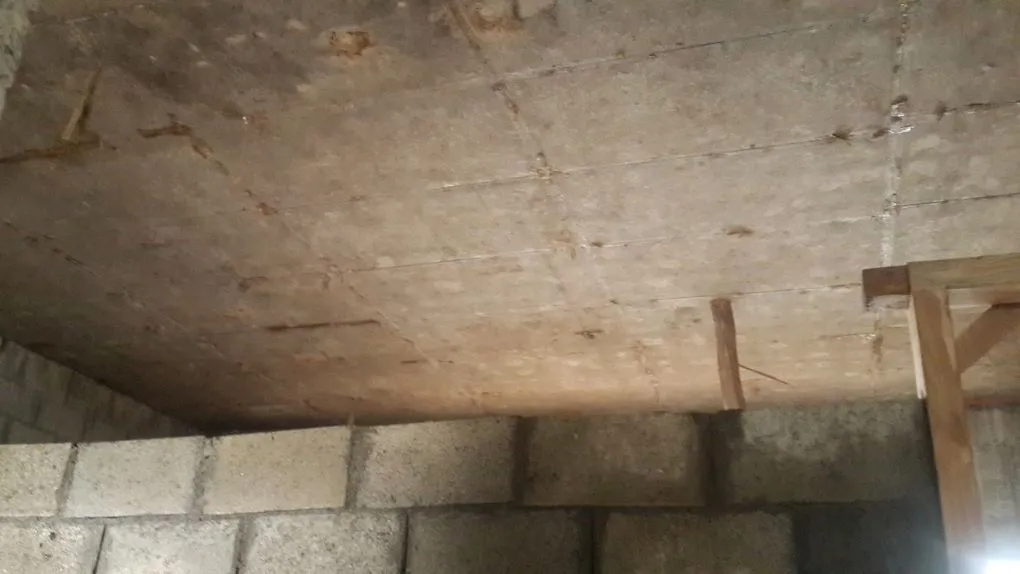
Spherical ribs have been provided under Crosslock spacers. Due to this they are not visible after opening of shuttering. This improves aesthetics structures and can reduce cost of finishing.
Increased strength, earthquake resistance & Durability
With crosslock spacers and rebar chairs, steel bars are the desired positions only. So there is proper transfer of strength from steel to concrete. This also means that at the of earthquake there are much lesser chances for the earthquake to find a weak spot to damage the structure. With better strength and protected steel bars buildings last much longer.
Long term cost effective solution
Although Crosslock has a higher upfront cost, but their long term cost effectiveness is undeniable. Fewer maintenance and repair expenses down the road combine with long life of buildings, ultimately saving you money in the long run. The initial investment in Crosslock pays off handsomely in terms of reduced maintenance costs and increased life of buildings.
Problems with traditional cover system
No Locking System
Traditional cover blocks do not have a locking system. So they can easily get displaced from their position during casting. This can lead to uneven placement of steel bars. This can result in uneven concrete cover, weakening the structure.
Prone to Breakage & Displacement
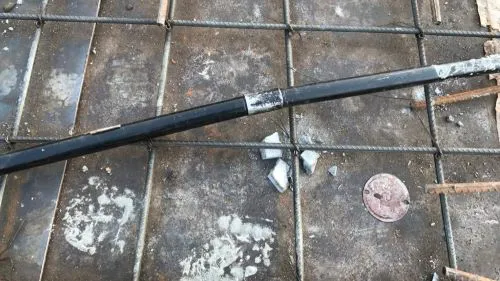
Conventional cover blocks are prone to breakage and displacement, as it can be difficult to ensure sufficient quality control to achieve the desired strength. Additionally, concrete has inherent tensile weakness, which can lead to breakage. This can result in uneven concrete cover, weakening the structure.
Does Not Mix in Fresh Concrete
Concrete once set does not mix in fresh concrete. So the preset cemented cover blocks does not mix with fresh concrete. This leads to cold joint formation, which can lead to structural problems.
Weak Spots
Traditional cover blocks can create weak spots in concrete structures, compromising their ability to withstand loads and environmental factors. They carbonate at a rate 5 times faster than structural concrete, which can lead to structural problems over time.
Porous
Conventional cover blocks are porous, which means that they can absorb moisture and chemicals. This can lead to corrosion of steel reinforcement and reduce lifespan of the structure.
Unsightly Concrete Finish
Traditional cover blocks can leave an unsightly finish on concrete surfaces. After the formwork is removed, the cover blocks can be seen on the concrete, creating a patchwork effect. This can be especially noticeable on large concrete surfaces.
Conclusion
Crosslock spacers and rebar chairs also known as PVC cover block offer a number of advantages over traditional cover systems, including improved strength, earthquake resistance, durability, aesthetics, and cost-effectiveness.
Applications
Different elements of RCC Crosslock spacers and rebar chairs are designed according to specific needs of different elements of RCC constructions. As different cover is required in specified in different elements, diameter of steel bars and the way they steel bars are tied is also different in different elements of RCC such as Slab, Beam, Column, footing and concrete wall.
Slab
In slab crosslocks are provided under bottom steel, beams, to steel / cranks / cantilever bars and electrical pipes.
Bottom steel
- Cover required = 20mm
- Suitable product = CL-20
- Accommodates Steel bars = 8mm to 12mm
- Recommended Spacing = 2 Feet
- Consumption = 25 per 100 Sq Feet
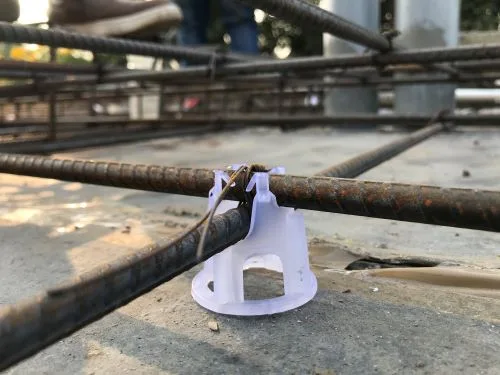
20mm clear cover is required in mild conditions. But this cover may be increased subject to environmental conditions. If cover is increased to 25mm, 30mm or 40mm accordingly CL-25, CL-30 or CL-40 can be used respectively.
Beam
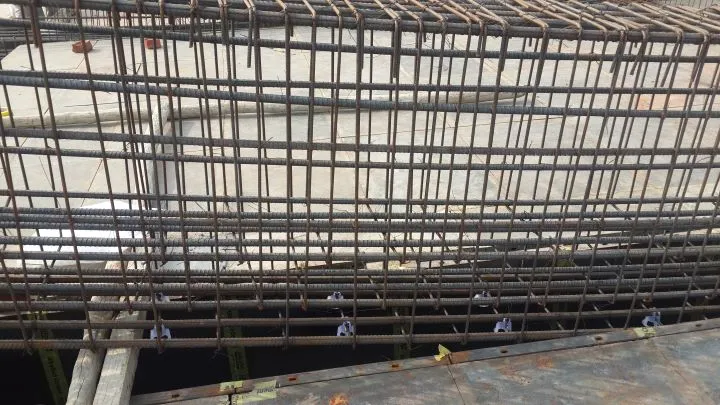
- Cover required = 25mm
- Suitable product = CLB-25
- Accommodate Rings = 8mm to 12mm
- Accommodate Main bar = Up to 25mm
- Recommended Spacing = 2 Pieces at the gap of 3 feet
- Consumption = 66 Pieces per 100 Sq Running Feet
25mm clear cover under beams is required in mild conditions. But sometimes cover is increased from 30 to 40mm. In that case CLB-30 or CLB-40 can be used respectively. CLB stands for Cross lock beams.
Double steel / Cantilever steel
- Cover required in 5″ Slab = 75mm
- Suitable product = CL-75 (3″ Rebar Chair)
- Accommodates Steel bars = Up to 25mm
- Recommended Spacing = 3 Feet
- Consumption = 5 per 100 Sq Feet
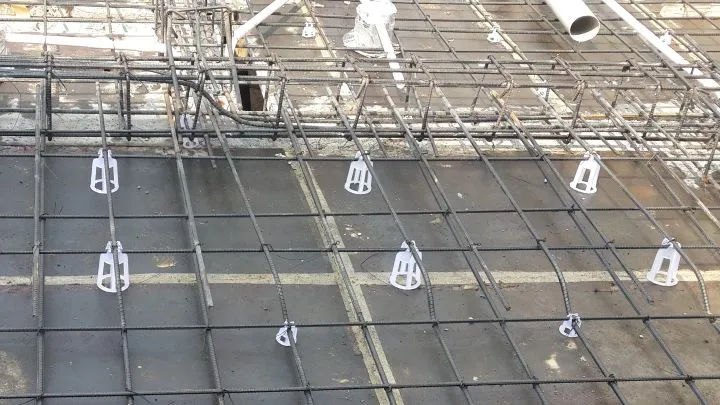
In case of 6 Inch slab cover required is 100mm and suitable product is CL-100 (4″ Rebar Chair)
Electrical Pipes
Cracks under pipes can be prevented by keeping in the center of slab, which is neutral zone.
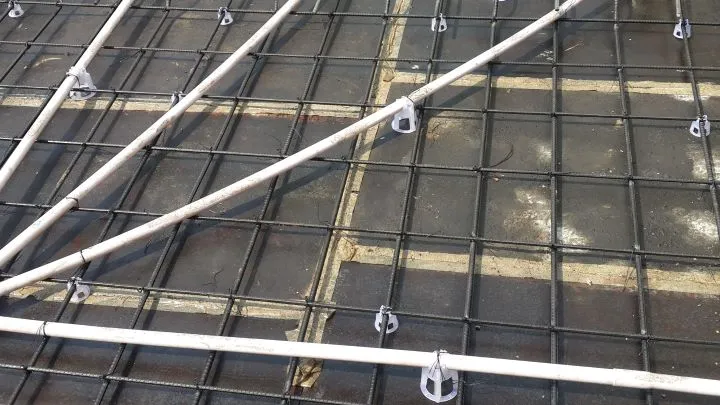
- Cover required in 5″ Slab = 50mm
- Suitable product = CL-50
- Accommodates pipe = Up to 25mm
- Recommended Spacing = 3 Feet to 4 feet
- Consumption = 4 per 100 Sq Feet
Column
- Cover required = 40mm
- Suitable product = CLB-40
- Accommodate Rings = Set of two rings of 8mm
- Accommodate Main bar = Upto 25mm
- Recommended Spacing = Apply on all sides of column at 3 Feet
- Consumption = 66 Pieces per 100 Sq Running Feet
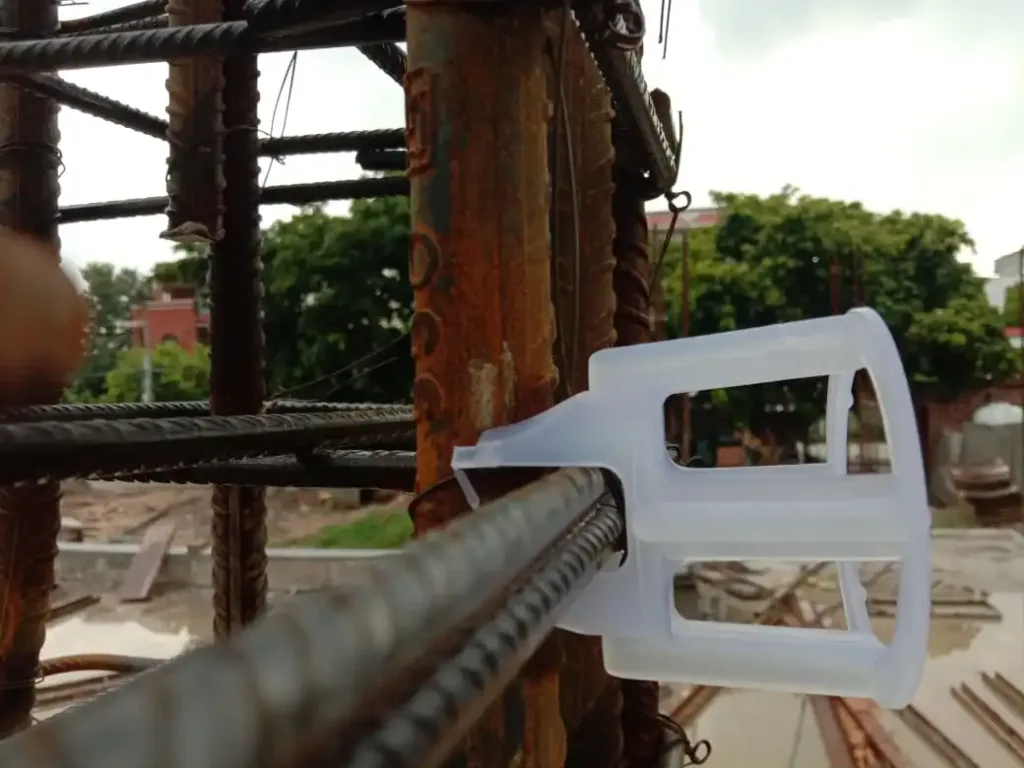
- Cover required = 40mm
- Suitable product = CLB-40
- Accommodate Rings = Set of two rings of 8mm
- Accommodate Main bar = Upto 25mm
- Recommended Spacing = Apply on all sides of column at 3 Feet
- Consumption = 66 Pieces per 100 Sq Running Feet
Sometimes when one of the sides of column is 9 inch than cover may be reduced to 25mm on that side. In such a case Spidrlock SL-2540 may be used. It’s two sides provides 25mm and one side provide 40mm gap.
Footing
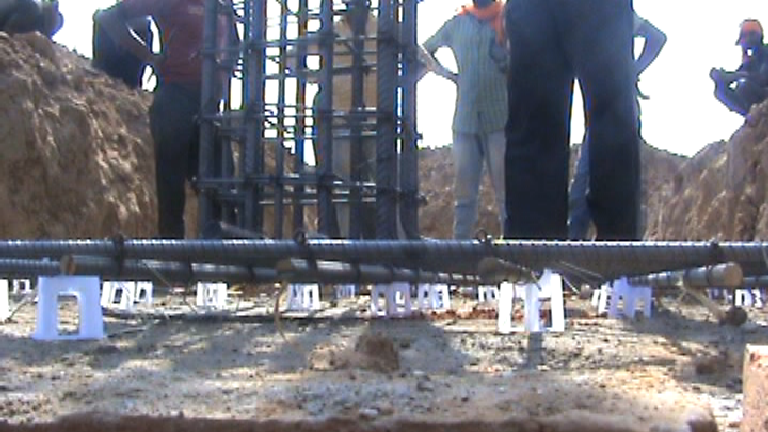
- Cover required = 50mm
- Suitable product = CL-50
- Accommodates Steel bars = Up to 25mm
- Recommended Spacing = 3 Feet + 4-5 pieces under the column
- Consumption = 13 per column for matt size up to 7×7 feet
Sometimes cover is increased to 60mm, 75mm or 100mm. Accordingly CL-60, CL-75, CL-100 may be used. Consumption can chance with size of steel net and in case of continuous footing.
Testimonials
Great experience
I used Cross lock spacers in 2013 in my first factory. We didn’t plaster our slab. Results were excellent. There were no ill effects. Now we are making an extension of our factory in 2020 and again we are using Cross lock. Everyone should use it. This is very good product.
~ Puneet Chopra, Exporter, Jalandhar
Best performance
Earlier I was using cemented cover blocks. But they used to get displaced when workers moved over it. So there were naked steel bars in the slab. Bars used to start corroding. I was not comfortable with that. I tried it on engineer’s advise. With it’s use steel bars stays at proper level, stays protected from corrosion and the slabs are flawless.
~ Prahlad Singh, Contractor, R.S Pura.
Solution for proper cover
Earlier there was cemented blocks, which used to break. That was not successful. So we choose Crosslock. It has got locking system and is a best quality product. Earlier we were using bricks and marble also. But that didn’t stay in place. Thanks to Crosslock my work is much easier now.
~ Mohan Lal, Masson, Jammu.
User’s Experiences
Installation Video
Get in touch
Location
MPLAST INDUSTRIES
Street no.3, Udyog Nagar
Gadaipur,
Jalandhar
Punjab
India
Phone : + 91 9814003839
Email : mplastindustries@gmail.com
Our Hours
MON-SAT 09:00 – 19:30